The digital factory 4.0
The digital factory and smart production management for Factory 4.0
Digital factoryThe call to optimize production processes is growing. The ability to adapt to meet the demands of your customers determines the degree of success for a producer.
In addition to customer demands such as quality, delivery time and price, your production must comply with regulations and standards and you want to work on sustainability. This can be done, for example, by using more environmentally friendly raw materials, minimizing your waste or making your production process more energy efficient. At the same time, you want to innovate to develop new products and maintain the flexibility to adapt existing products.
These goals together form a considerable challenge for production companies. One of the solutions that can help is to digitize the process. By replacing paper on the shop floor with an online environment, real-time insight is created that helps you shorten throughput times, reduce quality loss and increase delivery reliability.
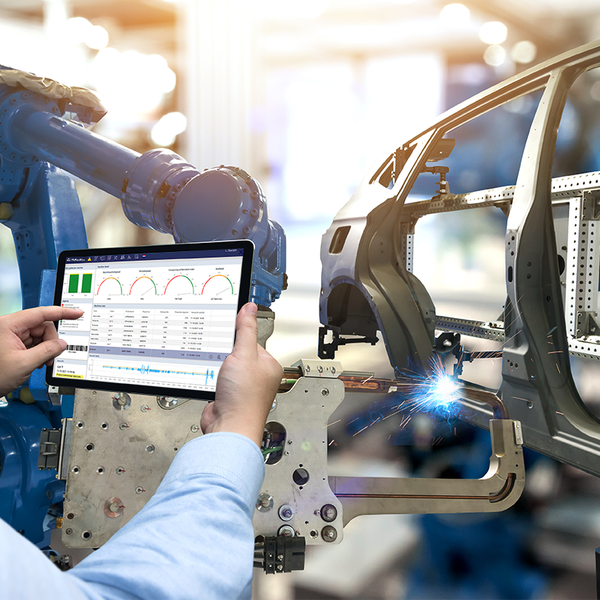
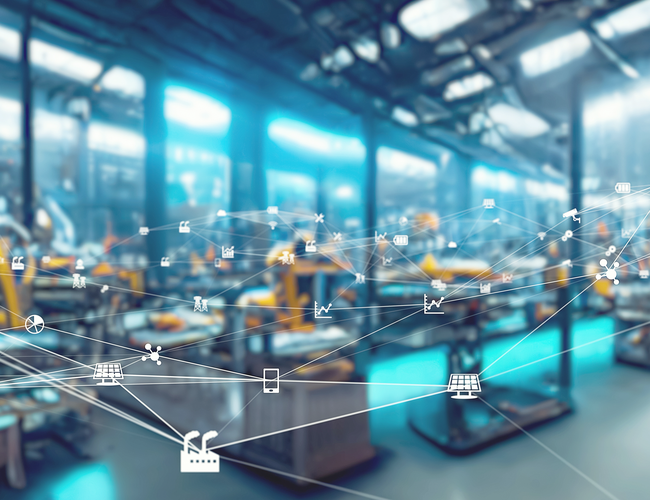
Perhaps you are familiar with the terms 'digital factory' or 'factory 4.0'. They represent a mature production process in which the exchange of information between different production components and physical locations is automated. In addition, a modern organization makes decisions based on generated data to continuously optimize the production process.
Organizations are looking for suitable solutions to digitize their processes. Due to the diversity of production processes and their management, the search often ends in a relatively expensive customized solution.
MyPlantFloor demonstrates that there is another way. This is a modular system that allows you to configure an affordable total solution in a relatively short time, so that you can achieve your goals with relatively limited resources.
On this page you will discover what the digital factory and smarter production management entail. We will also show you how an existing, fully configurable software package makes it possible to digitally control your production.