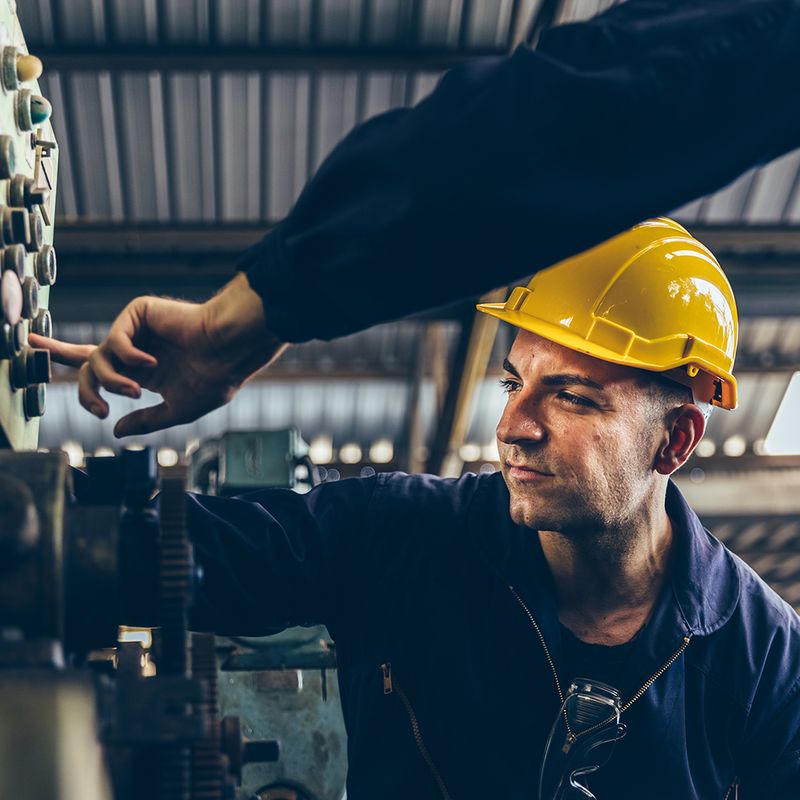
Maintenance Management
Many companies still see maintenance management as a cost item, while proper maintenance actually increases the uptime of a system and thus provides direct financial value.
Many companies still see maintenance management as a cost item, while proper maintenance actually increases the uptime of a system and thus provides direct financial value.
MyPlantFloor-CMMS (Computerized Maintenance Management System) is essential for an efficient and effective maintenance organization. The primary goal of this maintenance management system is to maximize the performance of installations at minimal cost. By centralizing all relevant information about installations and their components, MyPlantFloor's CMMS-system supports the optimization of work processes and contributes to a safe, reliable and available installation, with attention to the environment and the health of employees.
MyPlantFloor-CMMS distinguishes itself through its ability to integrate seamlessly with MyPlantFloor-OEE. These two complementary systems not only share the same database, but were also developed by the same team of engineers. Thanks to their uniform look and feel, they offer a consistent user experience, which considerably simplifies and strengthens the collaboration between maintenance and production.
The power of this integration lies in its unique ability to directly link maintenance costs to the increase in the degree of utilization (OEE). Where other maintenance management systems are often limited to recording malfunctions that are resolved by the technical service, the combination with MyPlantFloor-OEE provides insight into the full spectrum of production losses. This also includes minor downtime and inefficiencies that are handled by operators and therefore often remain out of sight of the technical department.
These in-depth insights allow companies to be more proactive in improving both technical availability and utilization rates, leading to lower maintenance costs and higher production efficiency.
By managing all important data and optimizing work processes, it increases the reliability and availability of installations.
MyPlantFloor - CMMS is characterized by the following benefits:
Operators with the right knowledge and access rights can directly carry out preventive work orders on the lines to which they are logged in. This saves time for the technical department and, more importantly, it increases the involvement of operators, reducing the number of malfunctions.
Thanks to shared production and maintenance planning, both departments know exactly when, for example, a major conversion is planned. This ensures more efficient cooperation and fewer unexpected disruptions.
The OEE system detects all losses, including minor downtime that often falls outside the scope of a traditional maintenance management system. This creates a more complete and accurate picture of the performance of installations. This information is important when deciding whether to repair or replace.
With access to exact data on operating hours and cycles from the OEE system, preventive maintenance can be planned more accurately. Operators can carry out inspection lists that, if necessary, initiate preventive work orders.
The standard mobile Maintenance Management app from MyPlantFloor-CMMS significantly improves the efficiency of maintenance organizations. This allows for faster troubleshooting and simplifies the maintenance process.
Important functions of the Maintenance Management app are:
Immediate malfunction notification: Every new notification appears within seconds as a work order on the mobile devices of the maintenance staff.
Automatic registration of working hours: Reduces administrative burden and ensures accurate time registration.
Direct access to documentation and data: All relevant information about the installation is directly available via the maintenance app.
Adding detailed photos supports work orders with visual information, which simplifies communication with suppliers and other parties involved.
Insight into spare parts provides direct insight into the availability of necessary parts on location.
On-site processing: Work orders can be finalized immediately upon completion, ensuring a streamlined process.
“A good mechanic fixes malfunctions, guarantees a safe working environment and always strives for the most efficient solution. He has technical knowledge, dexterity, creativity, problem-solving skills and stress resistance. Tinkering is a skill that is currently seriously threatened in many Western countries due to an aging population. Any form of efficiency improvement is therefore more than welcome.”
A well-thought-out preventive maintenance plan is essential for a well-performing installation. The challenge lies in determining the correct level of preventive maintenance. Too much maintenance leads to unnecessarily high costs, while too little maintenance results in unplanned downtime, expensive emergency repairs and loss of production.
MyPlantFloor-CMMS offers extensive options for accurately determining the timing of preventive maintenance. In addition to time-based activation, you can also choose criteria such as operating hours, cycles, behavior or combinations of these for each preventive maintenance task.
The maintenance management system also supports dynamic inspection lists, which – like preventive work orders – can be activated by various triggers. These inspection lists can be easily accessed via the mobile app. When an inspection does not meet the set requirements, a work order is automatically generated, possibly supplemented with photos and text to further clarify the situation.
Inspections not only play a crucial role in maintenance, but are also essential for the prevention of safety incidents and environmental damage within incident management.
The MyPlantFloor-CMMS Maintenance Management system has an advanced warehouse management system that allows you to efficiently manage your parts inventory.
Goods receipt: Simple registration of incoming goods.
Label printing: Fast and accurate labeling for efficient identification.
Location classification: Flexible allocation and management of storage locations within the warehouse.
Scanning: Support of barcode scanners for error-free and fast inventory management processes.
Order proposals: Automatic suggestions for restocking based on current stock levels and consumption data.
With these functions, MyPlantFloor offers a powerful solution for streamlining inventory management, minimizing downtime and optimizing operational efficiency.
MyPlantFloor - CMMS is suitable for use at multiple locations and offers support in multiple languages, which users can easily switch between online. In addition, you can submit an unlimited number of support requests. The maintenance management functionalities of CMMS software include the following as standard:
Setting up a Maintenance Management system can often be time-consuming, but with MyPlantFloor-CMMS, a lot of attention has been paid to simplifying this process. Thanks to a user-friendly interface and intuitive screen layout of the CMMS software, setting up and personalizing the system is considerably easier.
MyPlantFloor customers particularly appreciate the flexible screen layout, which shows exactly the information that is important to them. With MyPlantFloor-CMMS can be used both on-premise and in the cloud. You can get started quickly and immediately benefit from a system that perfectly suits your needs.