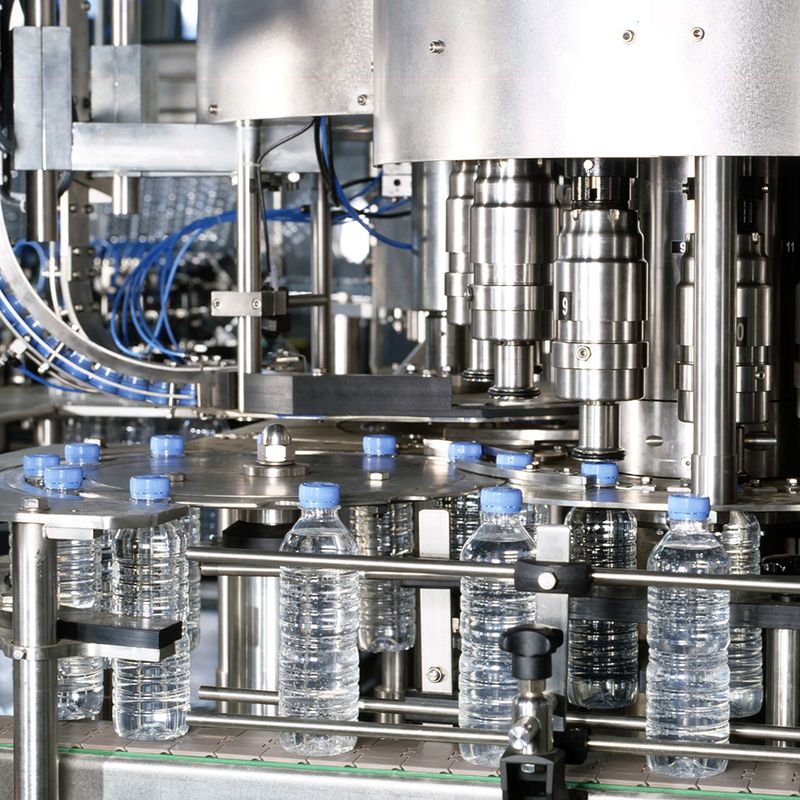
Lean manufacturing
Lean Manufacturing is nothing more than delivering good quality products or services on time, at the lowest possible cost. Lean originated from a logistics perspective.
Lean Manufacturing is nothing more than delivering good quality products or services on time, at the lowest possible cost. Lean originated from a logistics perspective.
In production, there is usually a chain of activities. The flow within that chain can run smoothly when there are no waiting times or intermediate and final stocks within the process. The pursuit of an optimal flow (shorten lead time) is therefore part of the basic principles of Lean, also known as 'lean production'.
Would you like to know more about Lean Manufacturing? Then click here.
· Less scrap and/or rework
· Fewer machine failures
· Lower inventory level
· Higher stock turnover rate
· Less space required
· Higher efficiency, more products per employee
· Higher delivery reliability
· Faster new products in the market
· Higher customer satisfaction
· More motivated employees
· Better relationship with suppliers
· Higher profit
· More sales
Initially, Lean Manufacturing was often applied within organizations whose production proceeds through a series of successive steps. In those cases, there are many sources of waste that can be eliminated, especially if the organization is part of a logistics chain. The goal of Lean improvement is to ultimately optimize the value stream within the organization. As much time as possible should be spent on value creation for the customer. All other activities are considered wasteful. Activities such as a supply chain, a production process or an administrative process. Lean Manufacturing requires a lot of attention from an organizational perspective. Problems must be tackled and everyone must help.
Contact us for more information about MyPlantFloor and how this product can enhance your Lean improvement efforts, or a free demonstration. Then contact us quickly on +31 76 5156572 or via info@agilitec.nl.
Discover MyPlantFloor