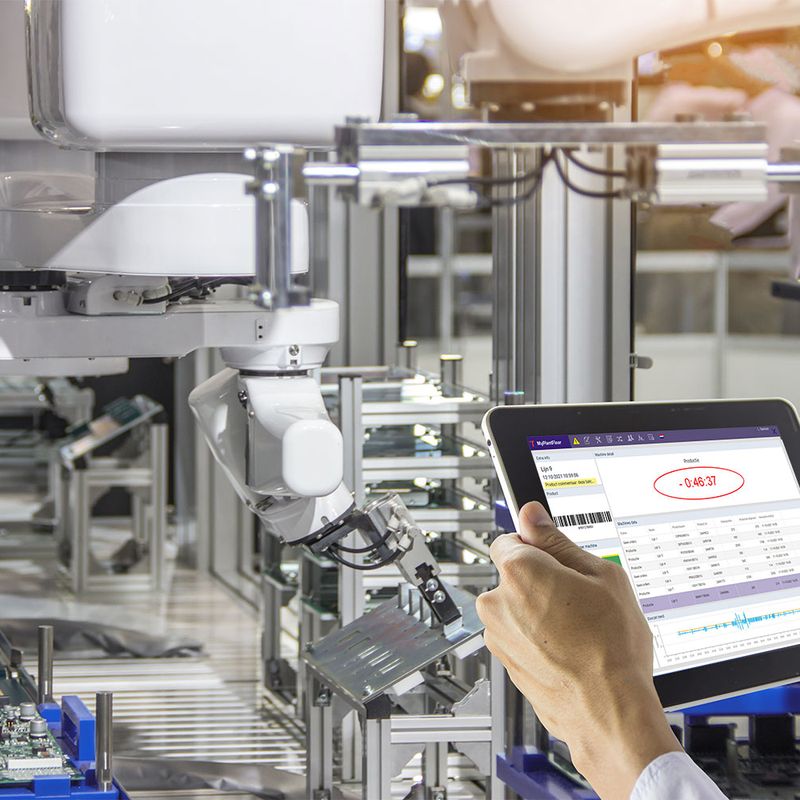
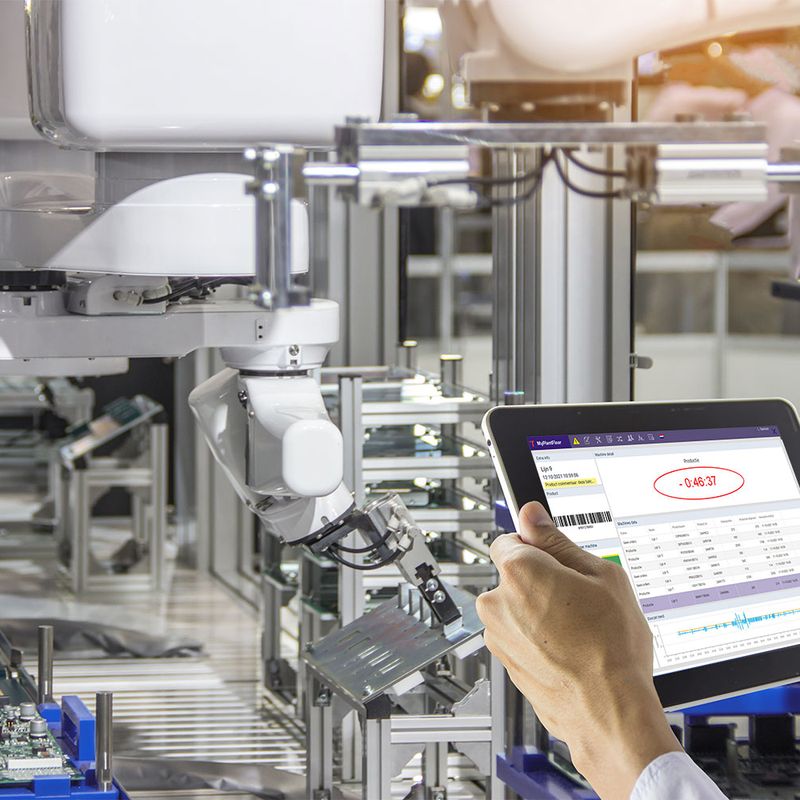
SMED Lean Improvement
Shorten changeover times with SMED-software
Single Minute Exchange of DieCustomer order-driven production is a frequently heard slogan these days. A short changeover time is an important condition for such a flexible production system. After all, means of production must be quickly and correctly changed over in one time. The SMED-method (Single Minute Exchange of Die) is a method to achieve significant time savings during changeovers. Every element of a changeover activity is analyzed and improved where possible. This way it can be seen whether it can be eliminated, simplified or streamlined. The essence of the SMED-method is to shorten the changeover time.
Single Minute Exchange of Die method
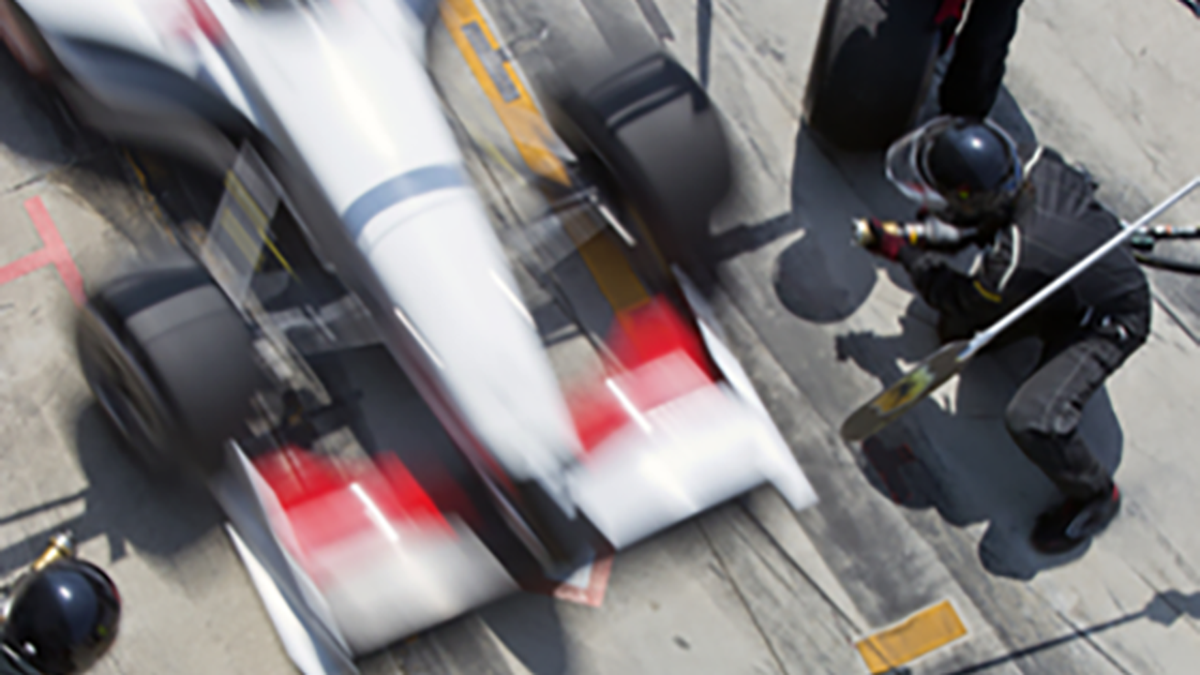
Simplify, eliminate and streamline
The SMED-method is a method to shorten changeover time. SMED was conceived by the Japanese Shingo, a Japanese industrial engineer and leader in the field of quality systems and production processes. Shingo believed that changeover time could be shortened to a few minutes, even if it currently takes several hours. The SMED-method is possible both manually and in machine-based production systems. MyPlantFloor is one of the few systems that can be expanded with a special SMED-Lean module. This SMED-module focuses on simplifying, eliminating and streamlining changeover activities, shortening changeover time.
Benefits of a successful SMED-method
· Shortening changeover times
· Lower production costs
· Optimized batch size
· Faster response to customer requests
· Fewer stock
· Improved startup routine
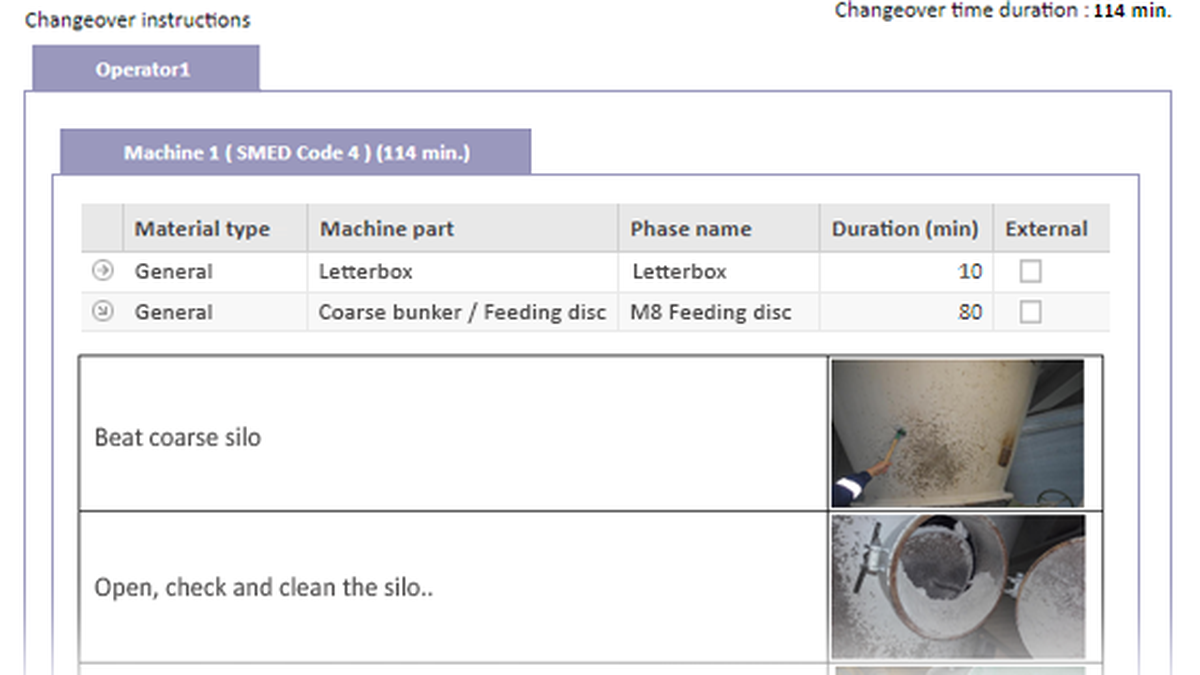
The 7 basic steps of the SMED-method
Observe the current changeover method and divide it into steps/activities
Separate internal and external steps/activities. Internal steps can only be performed when the machine is stopped. External steps can be taken while the machine is running.
Convert from internal to external where possible. Think of preheating tools.
Optimize remaining internal steps or activities and focus on connecting parts of the machine. Use a click system whenever possible.
Streamline the external steps or activities to match them with internal activities
Ensure new procedures are documented.
Make sure that the above steps are performed again. The changeover time must improve by about 45% per version. And multiple versions should lead to a changeover time of less than ten minutes.
Read more about the SMED-method
The SMED-add-on of MyPlantFloor
SMED-module from MyPlantFloor
When there is a wide variety of products, machines and operations, it is an impossible task to record an instruction or planned changeover time for each product transition. For example, with 100 products and five different machines, 50,000 transitions are possible!
Instead of a fixed definition for each transition, the SMED-module is able to generate a changeover instruction and planned changeover time based on differences between materials in the parts lists of two products. This method not only saves a lot of time when creating changeover instructions. The SMED-method of MyPlantFloor also offers a structured analysis and approach of each element in a changeover instruction in the form of a smart matrix, so that shortening changeover times becomes manageable.
Discover the benefits of SMED Software for yourself
Would you like to know more about MyPlantFloor SMED-software, shorten changeover times and the SMED-method? Or would you like a demonstration about production improvement? Check out all the info on the SMED lean method on the MyPlantFloor website. Contact us on +31 76 5156572 or via info@agilitec.nl.
MyPlantFloor - SMED